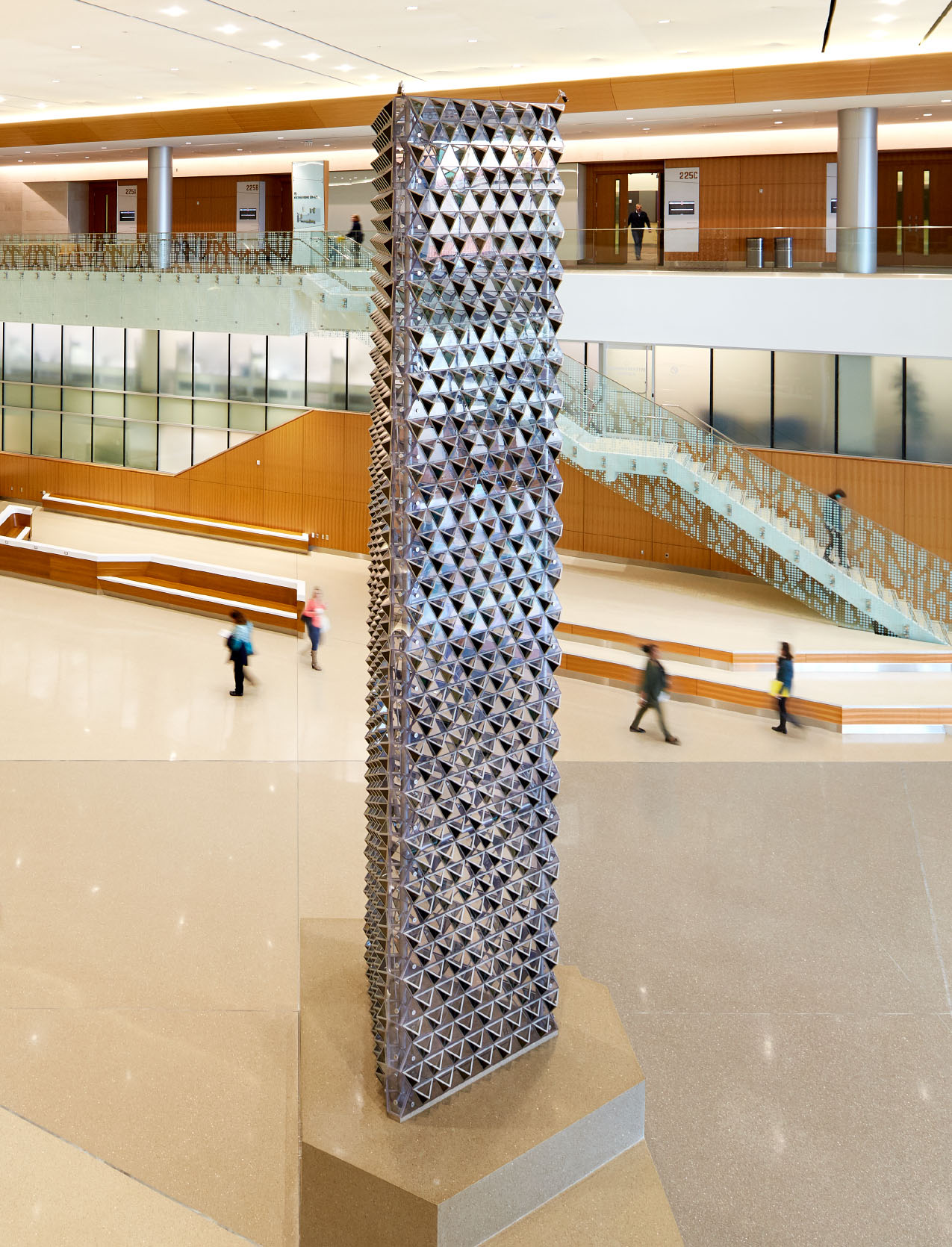
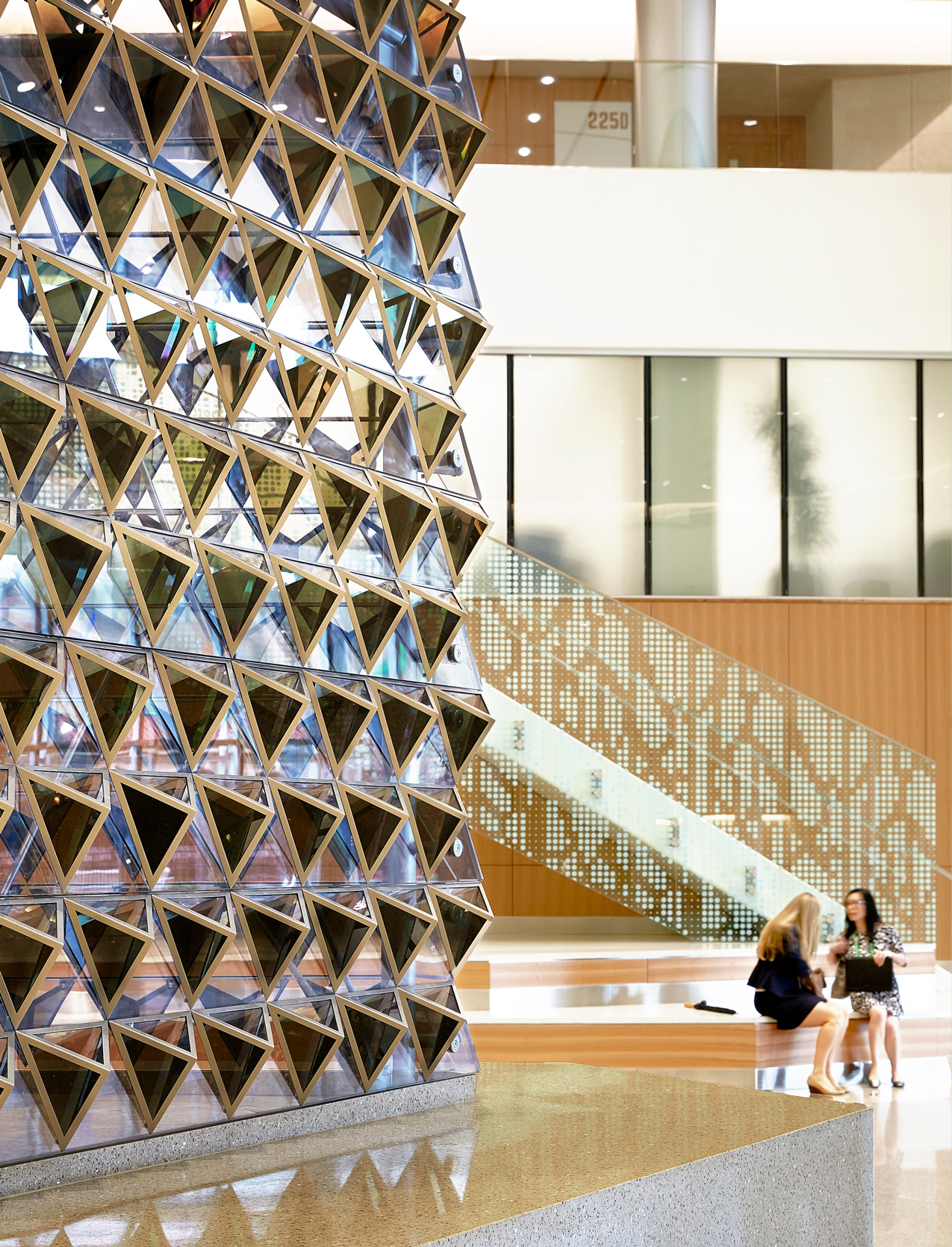
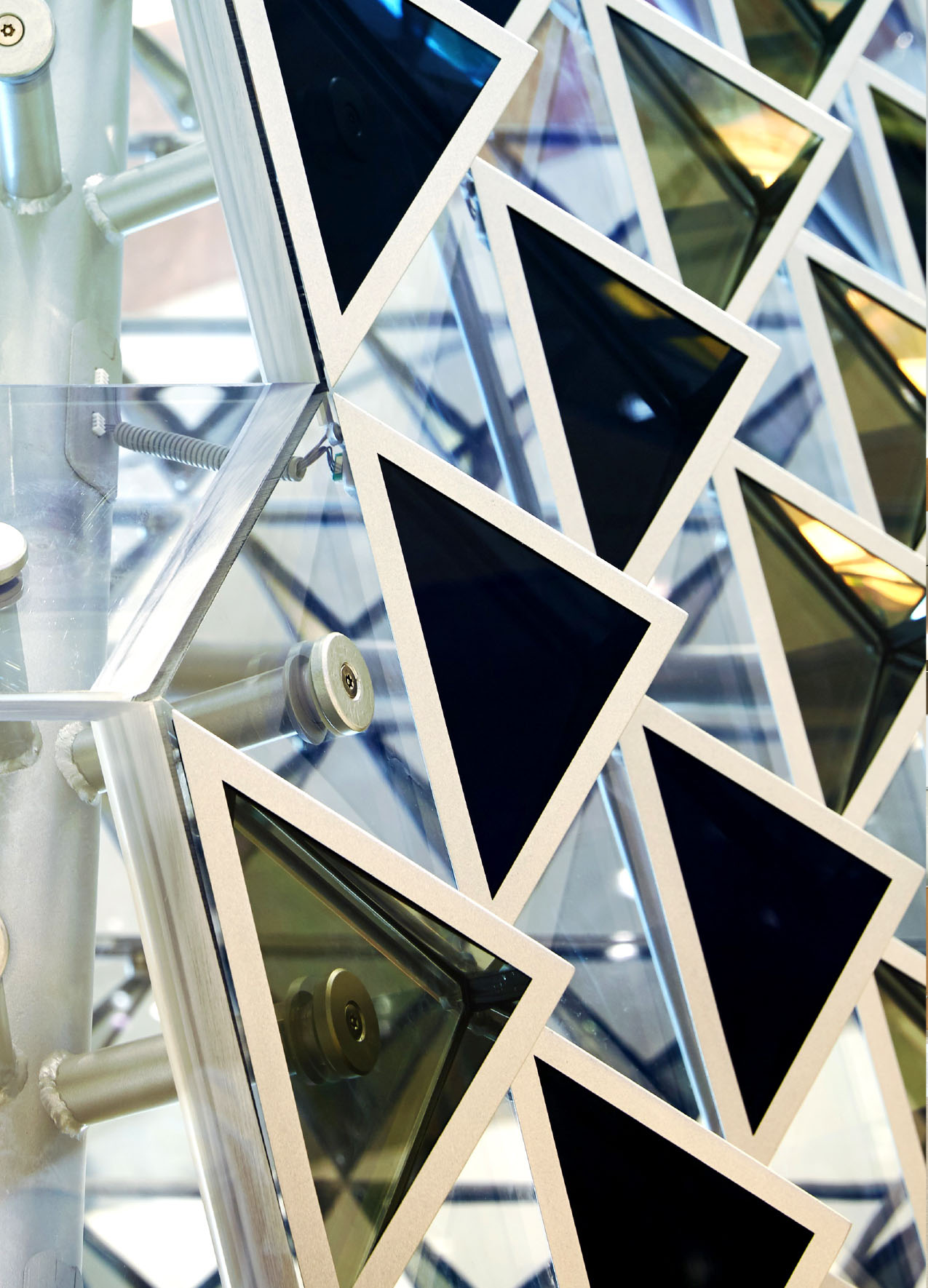
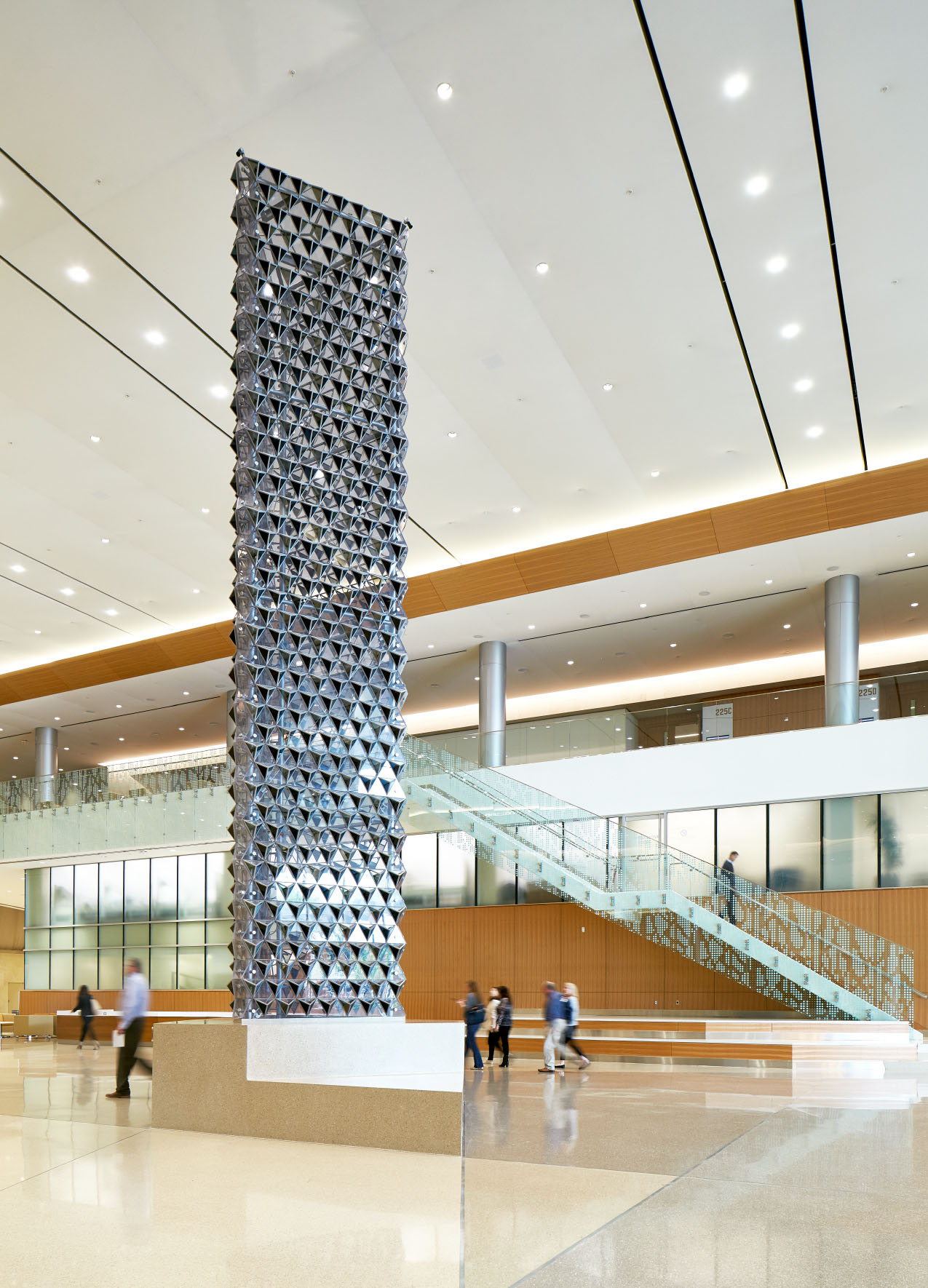
PROJECT “LIQUID CRYSTAL” LCD INTERACTIVE PUBLIC ART SCULPTURE, HENRY B. GONZÁLEZ CONVENTION CENTER, SAN ANTONIO, TEXAS
DESIGN JASON BRUGES STUDIO, UK
GENERAL CONTRACTOR HUNT ZACHARY CONSTRUCTION
PHOTOGRAPHY DROR BALDINGER
BUILT BY EVENTSCAPE, MAY 2016
Physical meets digital for this interactive art sculpture, recently unveiled at the Henry B. González Convention Center. Eventscape teamed up with Jason Bruges Studio of London, UK to bring this “Liquid Crystal” to life. Inspired by the flows of the San Antonio River and the flux of the convention center’s visitors, the sculpture interacts with a rippling, shimmering effect according to its surrounding activity.
The tower spans 32 feet high by 6 ft on all 3 sides, creating the piece’s triangularity. The main structure is composed of 3 vertical tubular steel struts with cross-bracing support. 132 steel standoffs were welded onto each vertical to hold the “skins” in place and house electrical. The skin, 1” thick polycarbonate panels, hold the steel framed LCD modular pyramids in place. These panels plug into individual circuit boards housed in the vertical struts which connect to the cameras installed on the top of the structure. These cameras monitor how many people move within the space and visually transmit the information down to each pyramid creating a transparent and opaque undulation. The more people in the space the more intense the pattern becomes on the tower.
Unique Characteristics & Project Challenges
Jason Bruges Studio did thorough R&D work prior to their relationship with Eventscape. The specificity of the custom triangular LCD screens drove the design of each individual pyramid frame, the panels and overall structure.
During the prototyping phase, the Eventscape team produced 12 different prototypes for the pyramid frames. Materials included aluminum, steel and corian using different technologies such as casting, milling and thermoforming, with the best material solution being 20 gauge steel. 990 pyramids were laser-cut to spec, brake-formed and welded with a robotic arm. 3D printed retention clips were designed and produced to hold the polycarbonate and house LCDs.
Eventscape managed the coordination between the three timezones in London, San Antonio and Toronto, using live video conferencing. This allowed Eventscape to show the designer and client the staged mockup in real time, discussing the details, interactivity and scale of the project.
In order to reflect its name, “Liquid Crystal”, the structure’s clarity was extremely important. Sourcing the polycarbonate material for the panels proved to be challenging, as the required 1 inch thickness seemed to vary in clarity with local suppliers, driving us to source the material in Europe. Hardware and weld connections were also under high scrutiny due to full visibility of the structure’s internal and external parts. The tolerance during fabrication was extremely tight, only allowing for 2mm.
To prevent moisture from reaching the delicate circuitry inside the pyramids, Eventscape tested various options. Custom cut neoprene gaskets and silicone strips proved to be most effective for waterproofing.
The structure shipped in two halves, wired and was pre-mounted. The 66 individual polycarbonate panels with 15 pyramids attached to each, were packaged in custom crates, each securely housed in custom slots. On site, Eventscape’s install team had to be extremely precise as the crane used to install the steel structure only cleared the ceiling by 6 inches.
With a challenging accelerated timeline of only five months from initial handover, through design and development, to fabrication, shipping and installation, time was extremely tight for each phase of this project. However the artist was extremely pleased stating:
“Jason Bruges Studio are delighted with the realisation of Liquid Crystal, which is in no small part a result of the hard work and dedication of the Eventscape Team. The artwork posed unique challenges in materiality, structure and technology, and required a fabricator that was not afraid to try new techniques and come to us with innovative solutions to design challenges. The working relationship was a close and collaborative one, and it was extremely reassuring to us that Eventscape had the same expectations as we did when it came to the details and quality of finish. The management of the project development, build and installation was extremely professional, and despite some hiccups such as the late arrival of some of the technical components, the team went the extra mile to bring the artwork in on time and on budget.
The quality of the completed piece is a testament to the team at Eventscape, and a reflection of the confidence which we hold for their professional approach. We would be delighted to work with them again and look forward to finding the next opportunity to do so.”
Jason Bruges