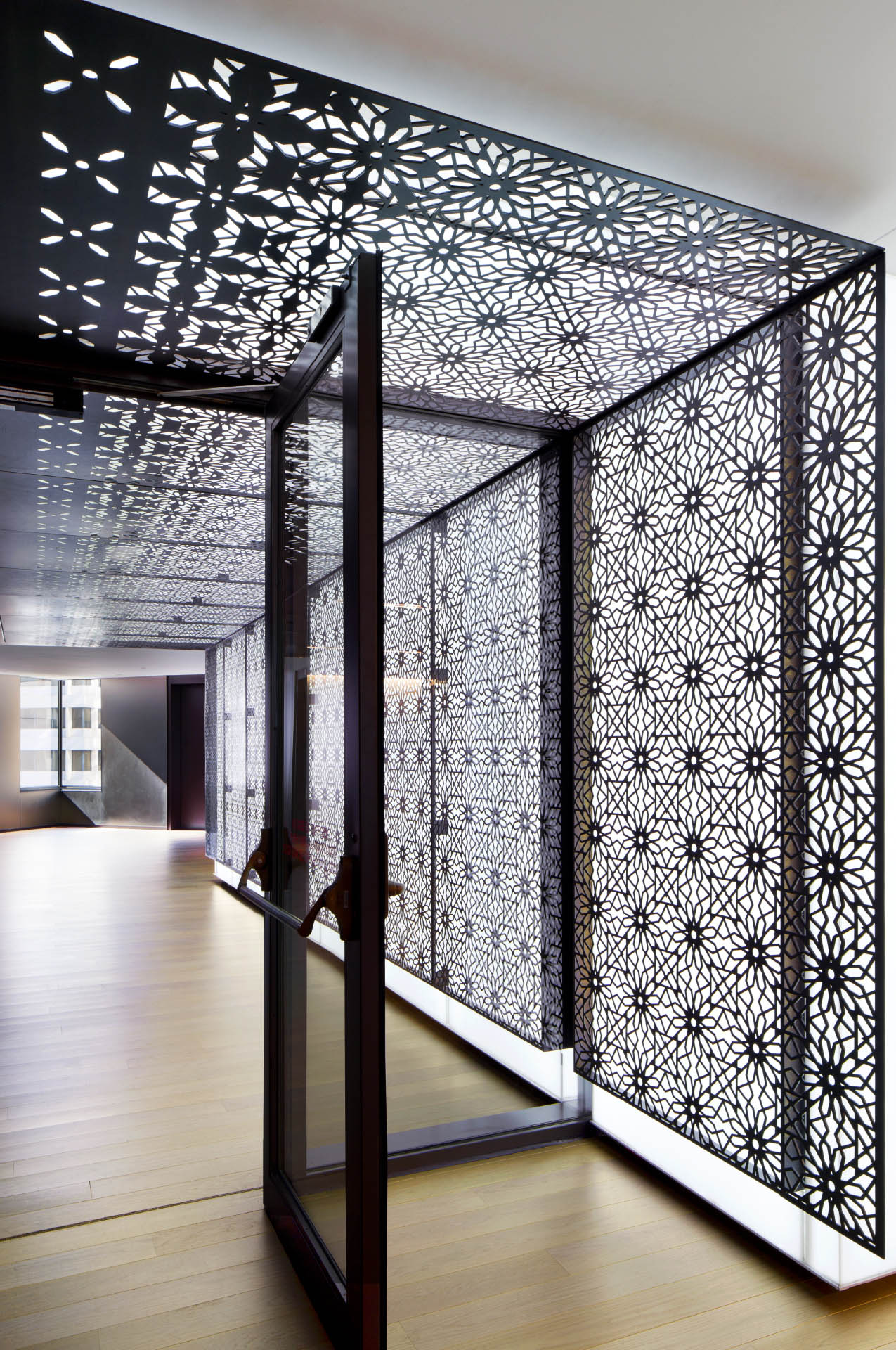
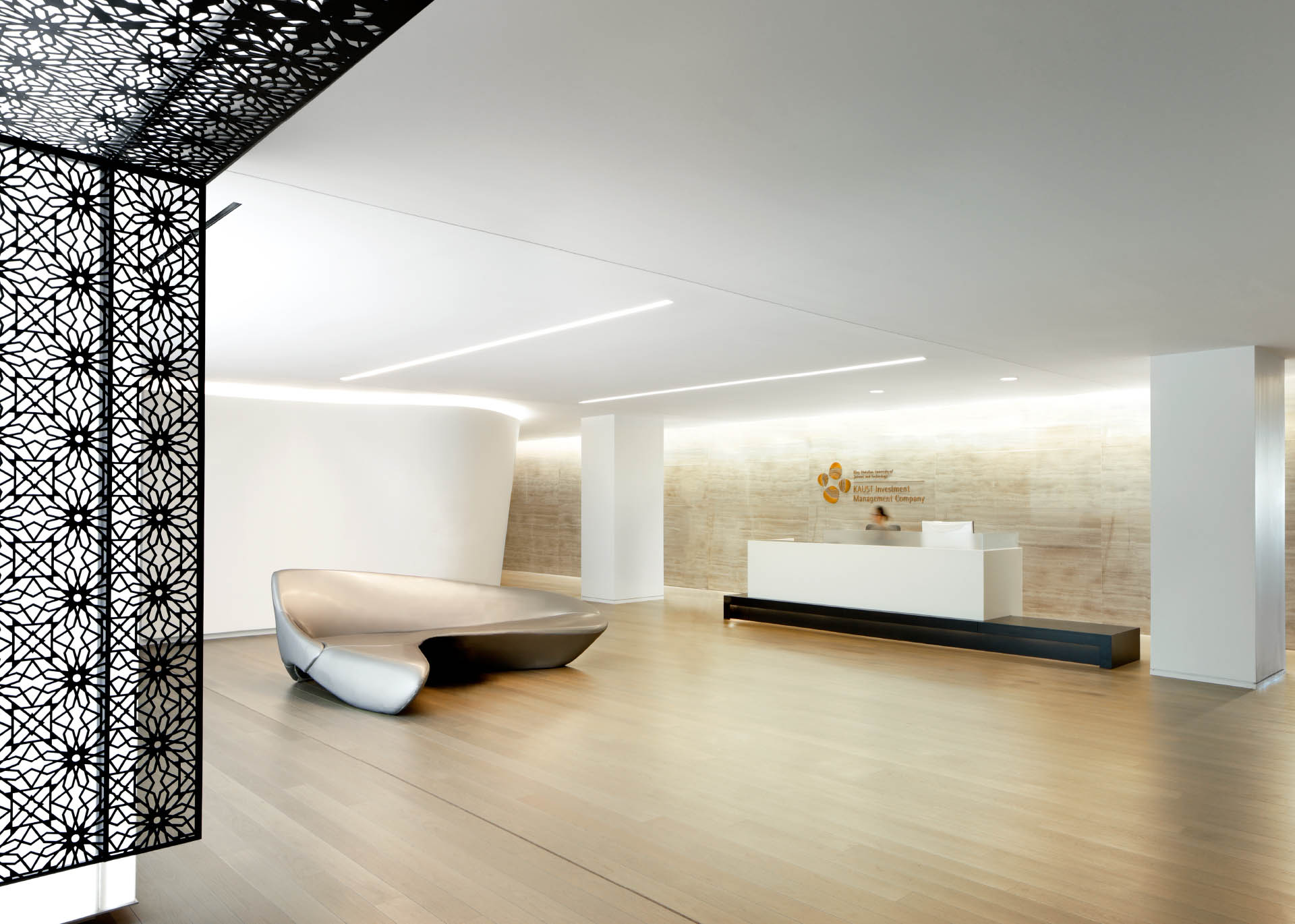
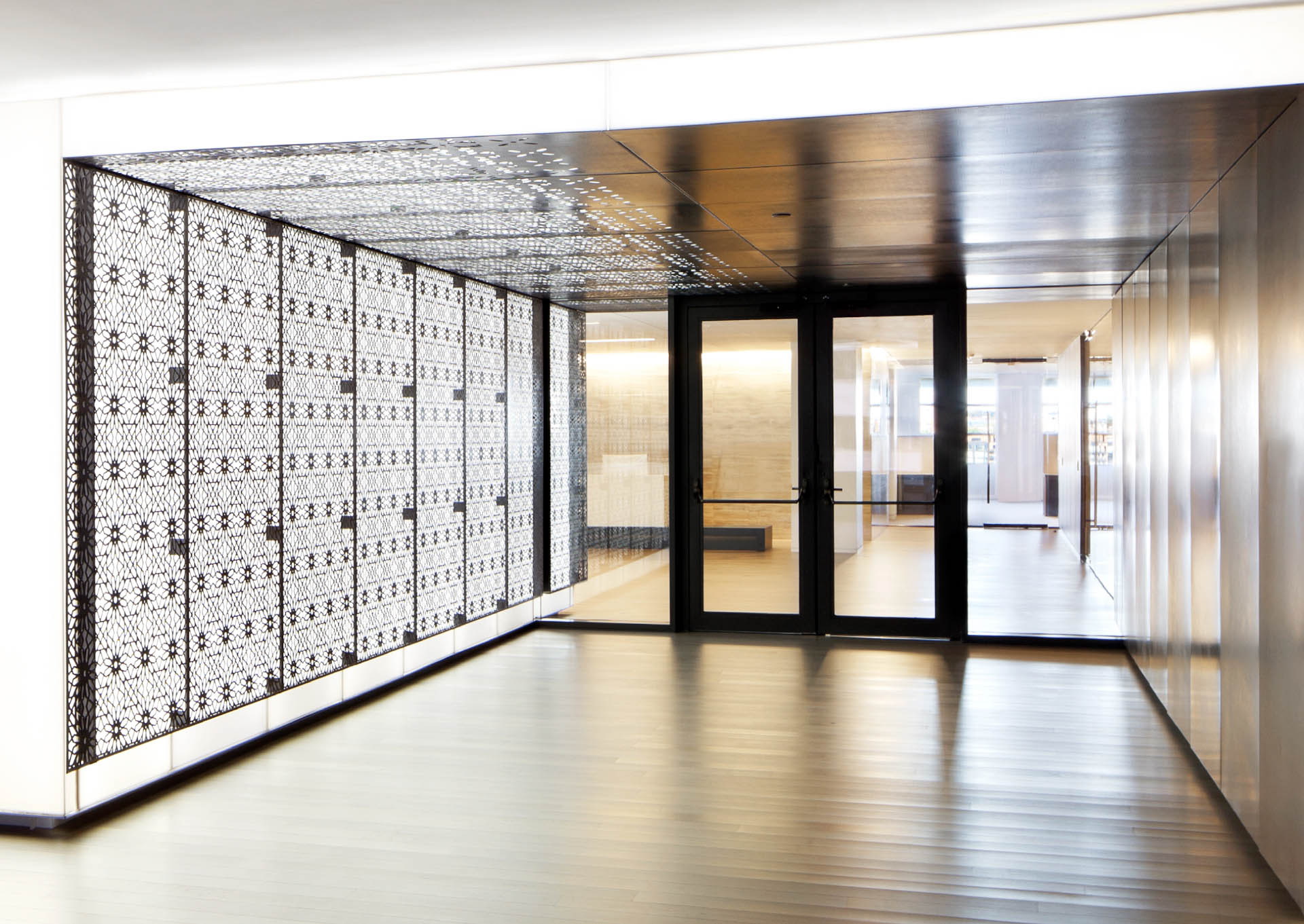
PROJECT KAUST INVESTMENT MANAGEMENT COMPANY, ARLINGTON, VA
DESIGN STUDIOS ARCHITECTURE
GENERAL CONTRACTOR HITT CONTRACTING
PHOTOGRAPHY BILYANA DIMITROVA
BUILT BY EVENTSCAPE, SEPTEMBER 2010
Eventscape fabricated several custom elements for this office space of the KAUST (King Abdullah University of Science and Technology) Investment Management Company. In the elevator lobby an ornamental thin profile polymer LED light wall and ceiling is overlaid with laser cut steel panels with a multiple layer bronze finish. The hand carved, double curved wall leading into the office helps to create a space of subdued elegance.
Unique Characteristics & Project Challenges:
The feature entrance to this office was built of a thin profile acrylic light wall covered with metal panels. Each steel panel is 4 ft. wide by 8 ft. tall with half of the 32 panels laser etched, and the other half laser cut with a custom Arabic motif. Beginning as an open screen, the design gradually transforms to the etched pattern on the facing wall. Laser cutting this tessellating pattern was very challenging as the size and intricacy of the pattern required over 1600 linear feet of cutting for each panel. In order to be programmed into the CNC laser, each panel had to be cut in a series of 2 ft. sections.
Eventscape explored multiple metal finish options to achieve the desired appearance. The solution was a hand brushed black oxide over bronzed steel panels with a clear lacquer top coat.
The architects required attachment with no visible hardware and a three inch offset from the light panel. Eventscape’s engineering team devised a custom reinforced steel connection that was able to support the 300 lbs of each LED/acrylic/metal panel unit, wrapping around to the back of the unit to connect to the existing wall. The ceiling installation was engineered to accommodate the ductwork above and incorporated sprinkler heads where required.
The feature double curved wall in the lobby area was built in two sections to allow for shipping and installation, and joined on site. Fabricated of wood with a fiberglass covering, each section was almost 40 ft. long by 8 ft. tall. The challenge was creating the compound curvature out of two dimensional surfaces; calculating the geometry required to retain a flowing shape.